Публикации
Влияние CFD на разработку инновационной технологии по уменьшению оксидов азота (NOx) в компании Fuel Tech

Введение
Fuel Tech, Inc является мировым лидером в предоставлении передовых инженерных решений в области контроля за загрязнением воздуха (Air Pollution Control (APC)) для электростанций (power plant utilities). Данные технологии по уменьшению оксидов азота (NOx) сейчас применяются по всему миру на более чем 800 объектах, предоставляя клиентам наиболее экономически эффективные (рентабельные) и экологически безопасные методы для производства энергии и переработки материалов. Недавно запатентованная технология Решетки для изменения угла входящего потока (Graduated Straightening Grid (GSG)), разработанная с обширным применением CFD моделирования, способна значительно повысить эффективность типового процесса Селективного каталитического восстановления (Selective Catalytic Reduction (SCR)) за счет оптимизации профилей скорости продуктов сгорания (отработанных газов, flue gas), потребления реагентов и времени жизни катализатора, при этом сводя к минимуму потери давления в системе.
Одно из первых применений установки GSG для блока 1 станции La Cygne (La Cygne Station Unit 1) в компании Kansas City Power & Light привело к экономии эксплуатационных расходов более чем на 5 миллионов долларов. Подобный экономический эффект был достигнут за счет снижения давления в системе, уменьшения накопленных частиц на каталитических слоях, меньшей эрозии и более продолжительного срока службы катализатора. Однако наибольший интерес и восхищение вызывает то, как именно Fuel Tech разработала данную методику и завоевала свою репутацию в промышленности. В данной статье читатель познакомится с разработкой GSG, являющейся частью всех новых SCR-проектов компании Fuel Tech.
Двигательный отсек является основным компонентом летательного аппарата AW609, так как он определяет производительность двигателя и обеспечивает безопасную...
Для рабочего процесса, начиная с импорта медицинских снимков (DICOM) и заканчивая 3D-визуализацией гемодинамического риска, использовались средства CFD и моделирования.
Рисунок 1: Общая схема оборудования по контролю за загрязнением воздуха (APC equipment) в энергоблоке камеры сгорания, работающей на твердом топливе
Предпосылки
Необходимость удовлетворять европейским директивам и новым правилам, предложенным Американским агентством по охране окружающей среды (U.S. Environmental Protection Agency (EPA)), обуславливает потребность в сокращении количества выбросов, что в свою очередь ведет к исключению с рынка ряда топливных ресурсов (включая уголь) из-за расходов, связанных с экологическим контролем (environmental control costs). Вместе с тем, экологические нормы, как правило, вызывают развитие новых экономически эффективных технологий для сокращения выбросов. В результате за последние десять лет первые применения моделирования при помощи вычислительной и экспериментальной гидро-газодинамики (CFD и EFD) биыли в области оптимизации систем контроля за загрязнением воздуха (Air Pollution Control (APC)).

Данные системы используются для сокращения выбросов от природного топлива (fossil fuel), на котором работают стационарные источники (электростанции и металлургические заводы). Наиболее распространенные из них наглядно изображены на рисунке 1 в виде общего расположения оборудования на электрогенераторной установке.
Технология SCR была разработана в 1980-х в Японии для эффективного сокращения концентраций оксида азота в продуктах сгорания (отработанных газах , flue gas) путем введения реагента аммиака (injection of ammonia (NH3) reagent) и реакции через каталитический слой (catalyst substrate). Целью данной разработки была стабилизация позиции угля на рынке, как наиболее экономически эффективного источника топлива.
Несмотря на относительно развитый характер технологии, существует ряд труднопреодолимых проблем, связанных с SCR-секциями электростанций, работающих на угле. Среди них:
• Минимизация потерь давления в системе с целью снижения энергопотребления вентилятора и эксплуатационных расходов электростанции.
• Достижение оптимального распределения скорости, NOx, NH3 реагента и профиля температуры для ввода в SCR реактор, позволяющих получить большую эффективность при сокращении концентрации и уменьшить количество используемого аммиака.
• Обеспечение одинаковых векторов скорости газа в катализаторе, с тем чтобы уменьшить риск его эрозии и, следовательно, продлить срок службы катализатора путем уменьшения его износа и деактивации.
• Предотвращение отсева частиц (particulate dropout) и накопления золы (ash accumulation) в SCR блоках, которые увеличивают потери давления в системе, время простоя агрегата для очистки, а также сокращают срок эксплуатации катализатора.

Рисунок 2: Типичная экспериментальная газодинамическая модель масштабом 1 к 10, тестирующая систему SCR
Благодаря недавнему значительному прогрессу в области вычислительной техники (computing hardware capabilities), инженеры Fuel Tech широко используют CFD для разработки устройств распределения потока (flow distribution devices), успешно решающих всевозможные вопросы, связанные с управлением SCR.
Компания Flow Tack и разработка GSG: Исторический взгляд
Flow Tack, LLC была основана в 2003 г. как инженерно-консалтинговая компания, применяющая CFD и EFD в качестве инструмента проектирования при разработке технологий по контролю за загрязнением воздуха (APC), включающих SCR, статические смесители, электрофильтры (ESP), рукавные фильтры (baghouses) и десульфурацию (процесс удаления серы) (desulphurization) отработанных газов. Традиционным устройством для оптимизации газодинамических процессов технологии APC был EFD (пример показан на рисунке 2). Однако, при использовании этого метода инженеры Flow Tack установили, что экспериментальное моделирование содержит в себе следующие недостатки и ограничения: с помощью экспериментальных моделей не происходит доступа к полному набору данных о полях течения, и инженерное исследование ограничивается конечным числом точек, в которых проводятся измерения. Всегда есть парадокс расположения дискретных точек измерения, требуемых для качественного определения потенциальных, заранее неизвестных, проблемных областей. Кроме того, существует потребность в высококвалифицированных экспериментаторах-специалистах, способных собрать и применить полученные данные. И, наконец, время, требуемое для испытания, корректировок и повторного испытания экспериментальных моделей в ходе оптимизации системы, становится ограничивающим фактором, особенно при необходимости соблюдения графика проектных работ.
По этим причинам Flow Tack стал ранним приверженцем CFD и содействовал продвижению этого уникального инструмента на рынке APC . Инженеры Flow Tack заметили, что рециркуляция происходила за счет конструкции типовых SCR-устройств распределения потока (typical SCR flow distribution devices), что не всегда было очевидно в ходе экспериментов. Обнаружилось, что подобные условия течения были причиной многих проблем, связанных с SCR-процессами. Также, использование CFD позволило удешевить разработку конфигураций устройства распределения с целью оптимизации профилей скоростей, входящих в катализатор и, таким образом, уменьшить вероятность накопления зольных остатков (ash accumulation). В соответствии с рисунком 3, целью создания технологии GSG было уменьшить количество горизонтальных поверхностей, предрасположенных к скоплению зольных остатков и тем самым обеспечить более плотную организацию пластин в решетке, что привело бы к более равномерно распределяемому сопротивлению и, следовательно, лучшему профилю скорости в катализаторе.
Помимо данного изобретения производительность GSG была проверена с использованием экспериментального моделирования динамики жидкостей (EFD modeling) с масштабированием 1 к 10. В первых итерации Сперва к удовлетворению компании Flow Tack экспериментальные результаты не повторили совпадали с результатами CFD результаты.

Рисунок 3: Диаграмма о GSG патенте США 8141588 B2 (Bible, Tan & Triece)
Улучшения в создании экспериментальных моделей и технологические достижения в CFD моделировании, такие как мельчение сетки в интересующих областях, в конечном счете привели к набору стандартов для обоих типов моделей, которые обеспечили достаточное согласие между результатами. С тех пор компания Flow Tack переходила от проекта к проекту и, при минимальных корректировках, используя процесс CFD моделирования, смогла оптимизировать конфигурации поворотной лопатки (optimized turning vane) для каждого проекта. В 2007 силами STAR-CD 3.24 Flow Tack параметризовал успешные примеры GSG и подал заявку на патент. Технология разрабатывалась дальше и дорабатывалась в последующие годы с использованием STAR-CCM+. В 2008 Flow Tack был приобретен компанией APC technology, Fuel Tech, Inc., которая также разрабатывает с помощью CFD технологию Селективного некаталитического восстановления (Selective Non-Catalytic Reduction (SNCR)). Обе компании имели множество смеж-
ных целей в продвижении разработки технологии SCR. Основной причиной приобретения Flow Tack была их значительная работа по применению CFD для разработки новых методов в смешении и оптимизации APC оборудования. GSG патент был подтвержден в 2012 и успешно применен на нескольких действующих электростанциях и промышленных объектах с SCR, начиная с 2009 (см. Таблицу 1).

Таблица 1. Успешные установки GSG с 2009 по 2014 гг.
Как GSG улучшает производительность SCR
Одной из основных проблем SCR являются частое выпадение твердых частиц и накопление золы на горизонтальной грани катализатора. Решением может быть остановка блока и периодическое удаление золы (vacuum the ash), что приводит к простою (downtime) и финансовым потерям (financial burden). Для контроля распределения скорости на грани первого каталитического слоя, в предыдущих конструкциях использовалось множество поворотных лопаток (turning vanes). Изменив их угол, положение и количество, инженеры и конструктора смогли улучшить распределение скорости на входе в катализатор. С целью контроля направления потока в сторону каталитического слоя, решетку для изменения угла данного потока (straightening grid) установили непосредственно над первым каталитическим слоем. Однако высокоточные результаты CFD-исследований позволили обнаружить образование рециркуляции отработанных газов (flue gas) и зон с низкой скоростью за поворотными лопатками SCR-системы, что и было вероятной первопричиной выпадения летучей золы на каталитические слои. Другим недостатком использования традиционной конструкции поворотной лопатки была ее чувствительность к условиям набегающего потока (upstream), что ужесточало требования к ее точному расположению и наклону (angling) в процессе создания SCR-системы для получения гарантированного совпадения результатов прототипа и модели.
Любые изменения в системе набегающего потока приводили к пересмотру модели и к корректировкам параметров лопаток для поддержания требуемых распределений.
В результате проведенной компанией Fuel Tech CFD оптимизации, появилась современная комбинация из группы поворотных лопаток (turning vane array) в изменяющей направление потока решетке (straightening grid) внутри конкретного GSG-устройства. GSG состоит из параллельных пластин (plates), установленных в SCR кожух (корпус, SCR hood) по диагонали. Такая конструкция необходима для вертикального перенаправления движения летучей золы (fly ash) и отработанных газов (flue gas) в первый каталитический слой, как показано на Рисунке 4. Данное устройство имеет меньшую чувствительность к распределению набегающего потока, что защищает катализатор и не оказывает влияние на его производительность даже в случае, если блок (unit) работает не в оптимальном проектном режиме (optimum design conditions).
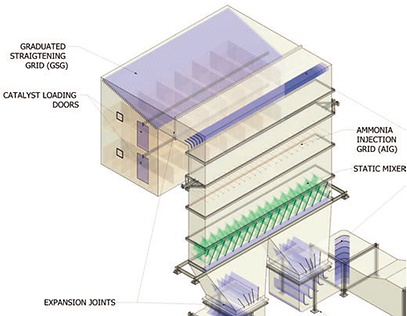
Рисунок 4: Типичный блок SCR с участком GSG, расположенным над катализатором
Применение GSG в блоке 1 компании LA CYGNE
Kansas City Power & Light Company (KCP&L) является поставщиком электроэнергии для клиентов в Канзасе и Миссури. Блок 1 (Unit 1) KCP&L’s La Cygne представляет из себя котел с циклонным предтопком 815-MW Babcock & Wilcox, с системой двухступенчатого сжигания топлива (overfire air) и блоком SCR. Блок 1 сжигает смесь (blend), состоящую на 90% из бассейна полибитуминозных углей бассейна р. Паудер (Powder River Basin (PRB)) и на 10 % из ресурсов местной угледобычи штата Миссури (local Missouri). По причине примитивной (poor)гидродинамической конструкции (fluid dynamic design), зола (ash) накапливалась внутри реактора SCR в среднем в количестве 1,450,000 фунтов в год, что приводило к значительным расходам на удаление золы, замену катализатора, понижение давления на катализаторе, эксплуатацию вентилятора, а также на реагент аммиака (NH3). Кроме того, компания La Cygne страдала из-за утечек аммиака (NH3 slip) (неиспользуемый реагент, который «ускользал» через неучаствующий в реакции катализатор) связанных со снижением активности катализатора. Увеличение объемов потери реагента приводило к эксплуатационным проблемам на выходе из реактора, включая снижение уровня давления в предпусковом подогревателе и в омывателях воздухонаг-
ревателя (over the air preheater and more frequent APH washings). В 2012 году скорость накопления золы возрасла вдвое по сравнению с обычным количеством, поскольку электростанция работала сверхурочно с низким коэффициентом нагрузки (demand factor). Хотя за предыдущие годы было сделано достаточное количество незначительных изменений по улучшению производительности системы, ни одно из них не было успешным, поскольку не затрагивало суть проблемы.
Однако технология GSG, разработанная и спроектированная компанией Fuel Tech, успешно решила все эти задачи и значительно улучшила конструкцию поворотной лопатки по сравнению с традиционной. В 2012 году Fuel Tech была нанята компанией KCP&L для выполнения детальной оптимизации с помощью гидрогазодинамических вычислений (CFD optimization) и проведения валидационных исследований с помощью EFD. Впоследствии KCP&L обратилась к Fuel Tech с просьбой организовать поставку оборудования и соответствующих эксплуатационных гарантий, основанных на результатах данных исследований. На Рисунке 5 изображен результирующий профиль газового потока на входе (inlet hood) в реактор.
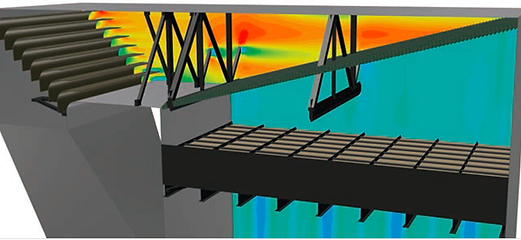
Рисунок 5: Контур скорости газа на входе SCR блока 1 La Cygne, в результате применнеия GSG
Данная установка была перезапущена в 2013 году со значительным сокращением уровня «зашлакованности» катализатора (catalyst pluggage), достигнутым благодаря выпадению золы в осадок (ash precipitation). Данное Такая модернизация (retrofit) была признана колоссальным достижением. Согласно данным инженера Скотта Хейдмена (Scott Heidemann) из KCP&L [1], применение GSG помогло ежегодно сэкономить на эксплуатационных расходах 5 миллионов долларов. Примечательно тажке, что следующая замена слоя катализатора для данной установки не предусмотрена по бюджету до 2019 года. Это означает, что в следующие 7 лет необходимо заменить только один слой катализатора, что является значительным улучшением по сравнению с заменой 8 слоев в течение предыдущих 5 лет.
FUEL TECH И ПОЯВЛЕНИЕ I-NOX
Комплексное снижение оксидов азота (Integrated NOx Reduction), или сокращенно I-NOx, является передовой технологией удаления оксидов азота и успешно решает ряд вопросов, связанных с SCR-установками. Это позволяет вывести SRC на более высокий уровень производительности при сохранении незначительного объема капитальных вложений (capital cost). Данная технология впервые была представлена компанией Fuel Tech как комбинация поэтапных методов, основанных на гидрогазодинамических вычислениях по сокращению оксидов азота. Она включает в себя передовые модификации процесса сжигания топлива (combustion modifications), состоящие из горелки со сниженными выбросами оксидов азота (Low-NOx-Burners (LNB)) и вторичного воздуха (Over Fire Air (OFA),), а также методы дожигания путем денитрификации (post combustion de-NOx approaches), включающие Селективное некаталитическое восстановление (Selective NonCatalytic Reduction (SNCR),) и Селективное каталитическое восстановление (Selective Catalytic Reduction (SCR)). Эта технология также позволяет оптимально использовать высокоэффективные устройства распределения потока, такие как статический смеситель, сконструированная по заказу специальная решетка для впрыска водного раствора аммиака в газовый поток (Ammonia Injection Grids (AIG)), и GSG. Анализ с помощью вычислительной гидрогазодинамики дал возможность инженерам заранее решить, какие подходы необходимо использовать на каждом из этапов проектирования. Существует множество факторов, способствующих достижению оптимальной конструкции. Например, критичными являются данные о непрерывном спектре (континууме) распределения концентрации окиси азота и аммиака, температурном и скоростном режимах (velocity patterns). Если профили (profiles)сильно отклоняются (skewed), инженеры могут произвести анализ с помощью гидро-газодинамических вычислений для определения количества смесей, необходимого для получения однородного распределения (homogenous distribution). Если профили (profiles) относительно хорошо распределены, то возможно будет достаточно настраиваемой решетки для впрыска аммиака (AIG) без необходимости использования смесителя, который увеличивает потери давления (pressure loss). Более того, использование GSG обеспечивает оптимально распределенные скорости однородного газа в ограниченном пространстве катализатора. Соответственно, благодаря технологии удаления оксида азота и устройствам распределения потока (AIG, статический смеситель и запатентованную GSG - технология компании Fuel Tech), SCR системы могут быть полностью оптимизированы.
Каждый из этих компонентов по сокращению оксида азота оптимизирован путем систематического применения передовой вычислительной гидро-газодинамики, которая дает возможность инженерам использовать метод проектирования в масштабах системы (system-wide design approach). Это позволяет в значительной степени сократить затраты по сравнению с использованием морально устаревающих традиционных автономных SCR-устройств и производить последующую диагностику проблемных областей по мере их появления. Было установлено, что стоимость I-NOx, при возможности достижения 85% уровня денитрификации (de-NOx), меньше, чем половина капитальной стоимости автономного SCR (I-NOx has been estimated to achieve de-NOx rates of up to 85% at less than half the capital costs of stand-alone SCR). По оценкам стоимость с учетом монтажа находится в диапазоне 100-150 долларов за 1 кВт за установку I-NOX против 300 долларов за 1 кВт за полную автономную SCR. На углесжигающей электростанции в Гонконге многие элементы I-NOx были успешно внедрены и помогли улучшить все рабочие характеристики блока (performance criteria). Благодаря закрепленному в Гонконге успеху, Fuel Tech продолжает получать огромное количество заказов от предприятий по всему миру на готовые модификации I-NOx (усовершенствование процесса сжигания топлива, SCR и SNCR).

Рисунок 6: Усовершенствование GSG в блоке 1 станции La Cygne компании KCP&L
ЗАКЛЮЧЕНИЕ
Быстрое развитие компьютерной техники и технологий вычислительной гидро-газодинамики (CFD) привело к появлению разработчиков уникальных инструментов контроля за загрязнением воздуха на электростанциях и других промышленных объектах (industrial facilities). Результатом является высококачественная система контроля за загрязнением окружающей среды, способная удовлетворить строгие экологические требования (meeting strict environmental regulations) при сохранении низкой капитальной и эксплуатационной стоимостей (capital and operating costs).
ЛИТЕРАТУРА
[1] Scott Heidemann, R. Thomas, D. Pfaff & D. Fischer: “Reducing SCR Fly Ash Accumulation with Improved Reactor Inlet Airflow” POWER, October 2013